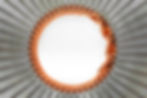-min_JPG.jpg)
Half the size.
Double the power.
Magnet Wire for all applications


Flat wire
Engineered for superior space efficiency and optimized for high power density, flat wire is ideal for compact and high-performance applications like electric motors and transformers.


Round wire
A versatile and reliable solution, round wire combines excellent conductivity with mechanical robustness, ensuring consistent performance across various industries and applications.


Hollow wire
Designed for advanced cooling solutions, hollow wire integrates fluid channels for thermal management in high-power applications, enhancing efficiency and reliability.


Concentric coating
Tau Group’s concentric coating ensures uniform insulation thickness around the wire, providing optimal electrical insulation and reducing the risk of localized breakdowns.


Eccentric coating
Specially developed for applications requiring tailored insulation, eccentric coating provides variable thickness to meet specific design and performance needs.
Technical specifications
Tau Group’s magnet wire is designed to meet the specific demands of our customers. With fully customizable solutions, we produce magnet wire featuring a monolayer coating that offers best-in-class dielectric properties, exceptional aging performance, a bending radius of ≤ 1.0 mm (for rectangular wire), and a record-breaking adhesion stripping force of ≥ 2.0 N/mm (PEEK).
Tau’s DryCycle coating technology enables the delivery of technopolymers-based (PEEK, PAEK, PEKK, PFA, PPS, PPSU) magnet wire tailored for high heat and voltage thresholds.
Geometry
Round wire: 0.7-8 mm
Rectangle wire: 1.5 – 50 mm²
Material
Copper: ETP1 and Oxygen-free (OF)
Aluminum
Nickel-plated
Silver
Polymer
PEEK
PPS/PPSU
PFA
PA 11/PA 12
Thickness
Ranging from 30 – 400 μm
-min.png)
Unparalleled performance
with DryCycle®
Tau has developed DryCycle®, a patented technology that balances the need for sustainable manufacturing with the power, reliability, and performance required by electrification. The wire manufactured through this breakthrough process enables the electric machines of tomorrow: more powerful, compact, and eco-friendly.
One-step process
DryCycle® redefines the efficiency, durability, precision and quality of magnet wire production. Our solvent-free, monolayer coating process offers three key benefits: it reduces operational complexity, minimizes environmental impact and enhances performance.
Two components
DryCycle® is compatible with both thermoset and thermoplastic polymers, allowing greater versatility in product development. With strategic partnerships throughout our supply chain, we are able to reduce lead times.
Magnet wire
Our continuous sensor monitoring alongside a marking system enables us to guarantee precision and accuracy throughout the coating process, thus ensuring compliance with specifications in the final product. We produce high-performance magnet wire.
Quality is part of our process
At Tau Group, quality is part of our process. We adopt a process-driven approach grounded in risk analysis and continuous improvement. This ensures that every product and service we deliver is compliant with customer requirements and exceeds industry expectations. Our team is committed to analyzing, monitoring, and refining processes to enhance efficiency and effectiveness, creating lasting value for our stakeholders.
Through a robust, ISO 9001:2015-certified Quality Management System, we ensure consistent compliance, continuous improvement, and adaptability to evolving market needs. By investing in skilled professionals and fostering a culture of learning, we empower our team to uphold excellence across every process.
We are ISO 9001:2015, IATF 16949:2016 and ISO 14001:2015 certified. We are also committed to implementing ESG reporting.
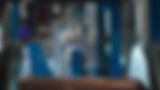